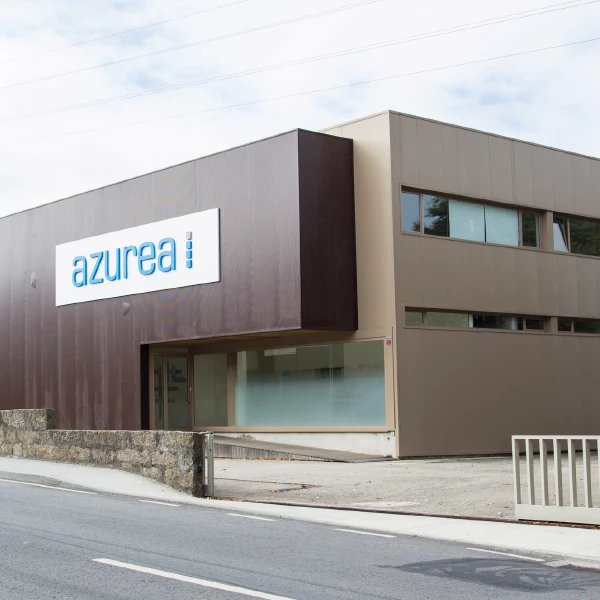
"Responding to the growing demand for capability with dimensionally centered parts".
"The work and exchanges with Ellistat over the first six months were very beneficial. Even today, if we have any doubts about a part, their support service is very responsive, and we get an answer within half a day. Regular updates ensure that the tool is constantly evolving. The ease of use of the software and the proximity to Ellistat are a real winning combination.
Vincent Skrzypczak
"The work and exchanges with Ellistat over the first six months were very beneficial. Even today, if we have any doubts about a part, their support service is very responsive, and we get an answer within half a day. Regular updates ensure that the tool is constantly evolving. The ease of use of the software and the proximity to Ellistat are a real winning combination.
Vincent Skrzypczak
History
The Azurea Group comprises four companies, three of which are based in Switzerland: Azurea Technologie Horlogere SA, Azurea Microtechnique SA (medical) and Azurea Jauges SA (metrology). The fourth entity, Azurea Unipessoal Lda, was established to support the Swiss companies and is based in Portugal (Porto). A brief history to remind us that the 1st company was founded in 1914 by Célestin Konrad, in Moutier (Switzerland - Bernese Jura). It originally specialized in the manufacture of watch components. In recent years, the company has created and acquired sites enabling it to expand and diversify under the name of Azurea Holding SA, and has been managed since 1995 by Mr. Daniel Uhlmann.
The key to success?
This development enables the Azurea Group to respond innovatively not only to the demands of the watchmaking industry, but also to those of the medical, dental -implantable, dental and device sectors. The Azurea Group is recognized in its respective fields for the high quality of its production of highly complex parts and assemblies.
The key to success?
Investments in high-quality production tools and the engagement of everyone, particularly around the APC (Automated Process Control) solution, which has been in use since 2020, guarantee more efficient production management.
Azurea Unipessoal LDA celebrates its 10th anniversary in 2022, with over 8 million euros invested in the Group's production facility, which boasts a total of 30 Tornos CNC bar-turning machine tools.
As Vincent Skrzypczak, CEO of Azurea Unipessoal LDA, explains: "The Group's values are innovation, independence, respect, ambition and success. The investment choices we make are technically oriented and dedicated to our customers. The Group has no sales force. The managers of the various entities are historically in direct contact with customers". As an example of innovation, he adds: "In the current context, we offer our customers services other than simply the manufacture of single components, but also more complex assemblies and functions. In addition, we make a lot of room for young people within the Group, particularly those coming from technical apprenticeships and engineering schools, in order to create a real dynamic and also to offer interesting prospects for development and careers".
Medical sector: stand out for the quality and complexity of your parts
In 2009, through the acquisition of a third-party company, we were able to optimize the division of roles between each company and focus on the medical sector.
While the watchmaking business is concentrated almost exclusively in Switzerland, the medical sector faces an ultra-competitive global market. It is therefore imperative for Azurea to set itself apart through the complexity and quality of the parts it produces.
Azurea Microtechnique SA is ISO 13485 certified and meets customer requirements in terms of traceability and validation of all production processes. Upstream of manufacturing, due to its complexity, implies significant preparatory work before the actual production of the part. Azurea is capable of offering a prototype run of 50 pieces before launching the production of several thousand units per year. Production constraints for parts and assemblies involve dimensional aspects, with tolerances within 5 microns, as well as aesthetic and functional requirements. The parts manufactured for the medical sector cover a wide range, from components for robotic surgery, to instruments for orthopedic surgery, to connectors for brain implants.
The search for a simple, intuitive solution to meet capability requirements
In 2020, to meet the evolving customer demands for quality and precision, the company was seeking a solution to ensure the renowned "Azurea quality" for internally manufactured parts and assemblies. A new trend was emerging where customers were beginning to request capability rather than just tolerances for dimensional specifications. This meant that derivations in manufacturing processes were no longer acceptable, and production had to focus on "centered dimensions".
The initial project, launched in Switzerland, sought out a software package to improve production control and monitoring, in an aim to ensure the aforementioned centered dimensions. On the recommendations of its service provider Ovale Performance (training) and consultant Jérôme Bilquey, Azurea chose the APC software solution developed by French publisher ELLISTAT, based in Haute-Savoie. The software was already recognized for its performance, ease to use, and intuitive interface.
Two APC licenses were tested in Switzerland, followed by two more in Portugal for a period od one month. The company looks at competing solutions, but they prove more complex to use and more expensive.
The APC trial period was paired with a week of training, led by the managers who then went on to train the rest of the setup staff. The goal of the team training was first, to explain the importance of the approach and the commitment to improving internal processes, and second, to highlight the advantages of working with centered dimensions to consistently deliver the same quality to customers, while also considering the satisfaction of the assembly department in receiving dimensionally centered parts for optimal assembly.
Implementing the solution providing support and engaging the team, took around six months. Azurea Unipessoal LDA was the first site to be equipped. As the company's CEO, Vincent Skrzypczak explains: "We want all our employees to be 100% committed to using the APC solution. In cases of poor programming, there was never a risk of hearing: "it's APC's fault". It required awareness, a shared understanding among users, ans recognition of the need for improvement.
APC is easy to use and intuitive, making it accessible even to non-specialist operators. APC is used for quick set-up and production monitoring. Vincent Skrzypczak emphasizes, however, that it is essential to have high-quality production tools (measuring instruments, machine tools, etc.) and that the preparatory work for the APC program is critical. For example, matching the number of tools to the number of correctors, indicating the dimensions involved, etc.
60 APC licenses for productivity and Azurea quality
Today, the Azurea Group has 60 APC licenses, one for each machine. Vincent Skrzypczak explains: "All you have to do is measure the part, enter the data into APC and it automatically makes all the necessary corrections at once. This makes our employees' work much easier. Before APC, if the drift remained within tolerance, the setup technicien had two options: recenter the dimension, or leave it as it was, within the acceptable limit. With APC, the dimension is always centred. We've achieved our quality objectives and improved productivity, as set-up time have been reduced by around 50 % and the company's overall scrap rate has dropped by approximately 30 %."
Moreover,, in the case of consistent drift on a machine, APC highlights that there is an issue in the machining process that needs to be addressed, completely eliminating the risk of operator error thanks to the software.
"APC has allowed us to produce the right quality," adds Vincent Skrzypczak. The software provides data on capability. If the results are poor, the process needs to be improved. Conversely, if capability is very high, it is possible to space our inspections. For some parts, we've gone from six checks per day to just three.
To go a step further, that is, to have corrections sent directly to the machine via APC, Azurea is waiting for the machine manufacturer to release the OPC-UA option.
Vincent Skrzypczak is also very satisfied with relations with the Ellistat team. "The work and exchanges with Ellistat, during the first six months, were of great benefit to us. Even today, if we have any doubts about a part, their support service is very responsive, and we get an answer within half a day. Regular updates ensure that the tool is constantly evolving. The ease of use of the software and the proximity to Ellistat are a real winning combination.