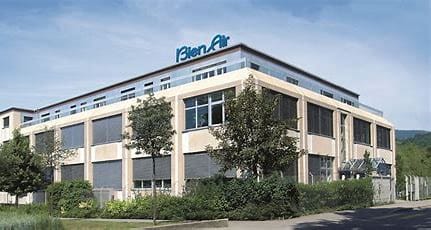
Bien-Air Surgery
Bien-Air Surgery optimizes its quality control efficiency with Ellistat's IQC Module
Request a demo"In my opinion, if you want to optimize control efficiency in the company, the only software solution to use is Ellistat. This is thanks in particular to the Artificial Intelligence built into the software, which enables you to control only what is necessary, automatically. If I had to do it all over again, I'd go back to Ellistat".
David Scarpino, CEO at Bien-Air Surgery
David Scarpino, CEO at Bien-Air Surgery
History
Founded in 2000, Bien-Air Surgery, now part of the Swiss Bien-Air Group, specializes in the production of surgical instruments renowned for their exceptional precision and reliability. Used by surgeons worldwide, these instruments are dedicated to the most sensitive areas of the human body (otology and rhinology, cranial, spinal). In 2018, the company is undertaking a reorganization process to gain in responsiveness, traceability, meet the growing demands for excellence in this cutting-edge sector. As part of a strategy to digitalize and redefine its processes, it is investing in production tools and control. It chose Ellistat's software suite (IQC and SPC modules), capable of managing all controls linked to the validation of production batches, and drastically reducing inspection times and returns to the workshop.
Bien-Air, founded in 1959 in Biel by David Mosimann, a precision mechanic and entrepreneur at heart, specialized in rotary instruments used by dentists. The company's innovative electric micro-motors quickly proved a great success. Since 1994, the company has been run by Vincent Mosimann, son of the founder, who perpetuates the family spirit and remains faithful to the original philosophy of simplifying the work of practitioners. The know-how and cutting-edge technologies developed by the company are also proving useful in the manufacture of other medical instruments. In 2001, the company became the Bien-Air Group, comprising two separate entities: Bien-Air Dental (300 employees) and Bien-Air Surgery (100 employees).
The market for surgical instruments is largely occupied by large, internationally renowned groups. However, Bien-Air Surgery is well established in this market. It stands out for its flexibility due to the size of the company, for the quality of its "Swiss made" products, for its cutting-edge after-sales service and, last but not least, for its open and transparent communication.
Bien-Air Surgery, "Swiss made" surgical instruments
The surgical instruments produced by Bien-Air Surgery are marketed in 80 countries by distributors. They feature high-speed micro-motors (up to 80,000 rpm), interchangeable handpieces in different shapes and sizes depending on the area of the body to be reached, single-use or reusable burs in a wide choice of shapes, materials (stainless steel, carbide, diamond, etc.) and sizes (up to 7/10th mm diameter for the inner ear and up to 9mm diameter for the skull), and burr blades for easy and safe resection of soft and hard tissues in rhinology. Finally, a console is used to manage the instruments. 70% of production is carried out in-house.
David Scarpino, co-CEO and COO, explains: "Bien-Air Surgery's policy is to fully satisfy surgeons with high-quality tools. Of course, we provide every guarantee in terms of standards, with over 10 audits every year. Innovation and cutting-edge technologies enable us to go even further and, for example, produce tools that don't heat up, don't vibrate, aren't noisy and have a service life of 8 to 10 years."
The production site is equipped with a dozen machining tools - machining centers, CNC lathes, screw-cutting machines - and state-of-the-art part inspection systems (dynamic 3D vision, for example). As part of its process improvement and digitalization drive, the company wanted to replace the three software packages it was using for incoming, in-process and out-of-process inspections, with a single package capable of managing all inspections.
Choosing software capable of managing all inspections
Bien-Air Surgery consulted three software vendors, and quickly realized that only Ellistat could meet its needs in terms of standards, ergonomics, traceability, flexibility, system customization and progressive control. Ellistat's IQC (Incoming Quality Control) module, designed to validate production batches from incoming inspection through to final inspection, is also very easy to access and program.
It is then necessary to assure that the software meets the stringent standards imposed in the medical sector, notably under the recent European MDR (Medical Device Regulation), with which all manufacturers will have to comply by May 2024, in order to be able to place their products on the market. The main areas of change, compared with the previous regulations, concern technical documentation, clinical evaluation and post-market clinical follow-up, as well as enhanced device traceability. The main objective is to ensure that nothing is delivered that represents a risk to the patient.
Ellistat, a team and software that adapt to the needs of Bien-Air Surgery
A year-long analysis of the risks associated with using the software was carried out, followed by six months of software development. Bien-Air Surgery and Ellistat work hand in hand to adapt the software to the needs of the manufacturer. Examples include digitizing all non-value-added operations (e.g. manual data entry, paper-based quality control, etc.) while seeking to optimize the process, proving the repeatability of the new control processes and guaranteeing data traceability for sixteen years.
I'm very satisfied with our partnership with Ellistat," comments David Scarpino. The flexibility of the software and the developments made by Davy Pillet's team enable us to work with software that is perfectly adapted to our company's needs, and not the other way round, which is a real luxury. We enjoy working with a young team who develop the latest generation of software, based on Web technology. Their solutions are innovative, easy to use, modular and ergonomic. The team is attentive, responsive and always available, even though they are increasingly in demand due to their success. What's more, they take our requests into account when updating the software."
More than promising results
Developments are still in progress, but Bien-Air Surgery has already seen a significant reduction in both inspection time and the number of inspections. It has seen a 10% gain in output (or man capacity), and expects 30% in the short term. This is thanks to the use of a single software solution (instead of three) and the elimination/digitization of manual operations. Ellistat's CES module also automatically adjusts the number of checks required to guarantee optimum results, based on initial inspection results.
To take this a step further, Bien-Air Surgery is deploying the SPC (Statistic Process Control) module from Ellistat's software suite, designed to monitor manufacturing processes in real time. The solution is also user-friendly and easy to use, particularly when it comes to parameterization, and fortunately so, given that the company produces some 5000 surgical instruments.
At this stage, Bien-Air Surgery has noted a 50% reduction in workshop returns for quality problems. The company is aiming for a maximum of 2% when the developments become effective, and even 0% when Ellistat's APC (Automated Process Control) module, dedicated to automatic machine-tool correction, is implemented.
David Scarpino concludes: "In my opinion, if you want to optimize control efficiency in your company, the only software solution to use is Ellistat. Not least thanks to the Artificial Intelligence built into the software, which enables you to control only what you need to, automatically. If I had to do it all over again, I'd go back to Ellistat.