For over forty years, SPC has been an integral part of the production environment. It is the statistical method for monitoring manufacturing processes.
The main objective of this technique is to monitor the behavior of a process. SPC is applied in production workshops with tools such as control charts. It helps to reduce scrap rates by anticipating non-quality.
The principle developed by Shewart and control cards allows you to apply an action to the process only when it's out of control. As long as I'm within my control limits in green, I don't correct my process, and as soon as I get out of my dispersion, I correct it.
SPC is a method that has long since proved its worth, starting with the automotive industry. SPC is still widely used today by manufacturers in a variety of sectors. However, setups are becoming increasingly complex, with interdependent dimensions. This obviously makes the job of the setter much more difficult than it used to be.
Case study : SPC in a watchmaking production workshop
Let's take a real-life SPC case from a watchmaking production workshop as an example.
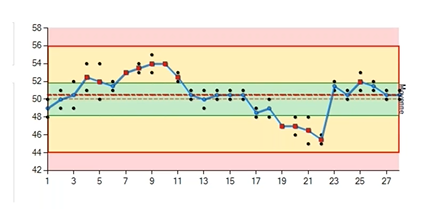
If you look at this control chart, you can see that a simple, basic SPC rule has not been followed. In fact, the process has been allowed to drift within tolerance limits. It's interesting to find out why. By digging deeper and talking to the setter on this production floor, we realized that this dimension had an impact on the next one. If the setter corrected this dimension, the next one would be bad. So, by choice, the setter stayed within tolerances. Unfortunately, this results in a quality that is not always optimal, and therefore does not meet customer requirements.
APC (Automated Process Control) as an alternative to the SPC to cope with control difficulties on the production floor
Faced with these difficulties, we need to find a solution capable of responding to the three main challenges facing manufacturers today:
- Challenge 1: master long-term capability
- Challenge 2: manage complex parts in a multidimensional environment
- Challenge 3: integrate into the digital chain
Automated Process Control (APC) is a concept invented under the direction of Prof. Maurice Pillet by thehe SYMME laboratory at the Université Savoie Mont Blanc. This is an evolution of SPC. APC consists in using IT resources to control a production process, in order to obtain much better quality results than with traditional SPC. By simultaneously adjusting dozens of correctors, APC corrects drifts using a damping function derived from a machine learning algorithm. The correction then drifts less towards the limits of the control board. This is because the correction is centered on the target functional dimension. In this way, quality is controlled over the long term.
Conclusion
Of course, the SPC still has its place on the shop floor. Today, however, there are developments capable of supporting set-up personnel in the correction of multi-dimensional processes. All the while integrating with Industry 4.0: this innovation is called Automated Process Control.