SPC software
Statistical Process Control
Monitor your manufacturing processes in real time.
Request an SPC demo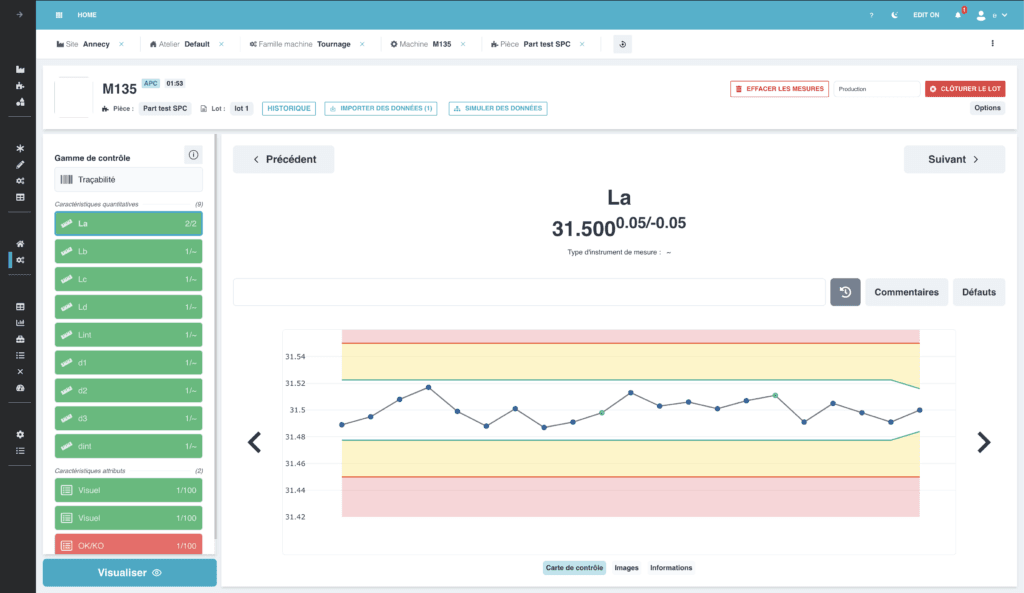
Visualize all your production data simply and instantly
With Ellistat's SPC software module, you can calculate your production capabilities and create control charts. Receive real-time alerts on process drifts, and reduce non-quality costs.
Our powerful SPC module is intuitive and easy to deploy.
Our Strengths
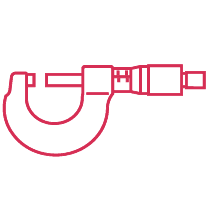
Connection to Measuring Equipment
Automatically import measurement data into Ellistat, whatever the communication protocol (USB, Bluetooth, RS232, .txt files, etc.), to avoid manual input errors.
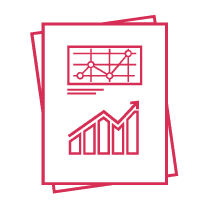
Customized Reports
Create your own report templates to provide customized data for each of your customers.
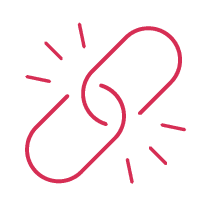
Link With the Module Data Analysis
Switch all your production data in 1 click to a powerful statistics module.
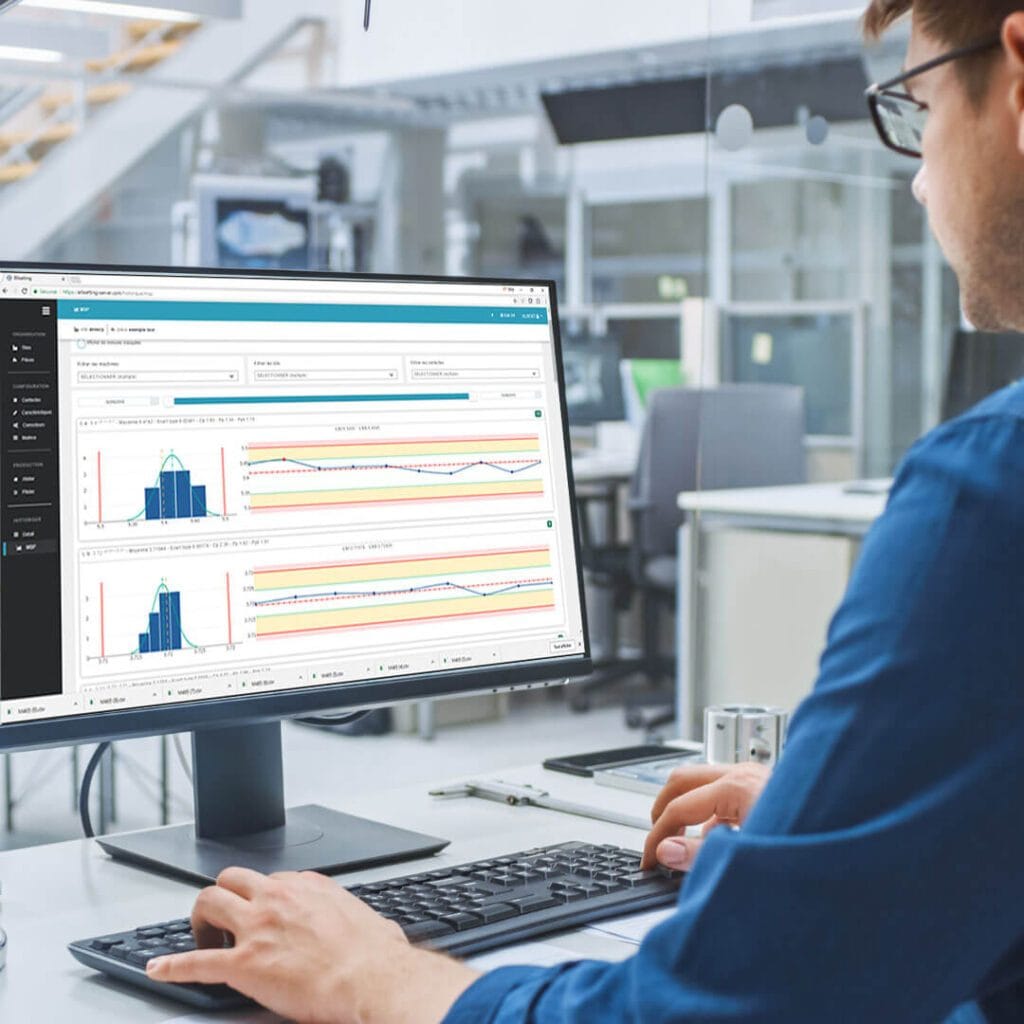
How does SPC software work?
A plug & play solution: connect your measuring equipment directly to the SPC module, whatever the connection mode (Bluetooth, USB, RS232, CMM...), and benefit from real-time process monitoring.
Read MoreEllistat offers advanced features for statistical analysis of your production (capability: Cp, Pp, Ppk, control charts, etc.) and automatic report generation.
We've thought of everything to make your life easier!
SPC Key Features
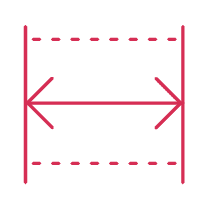
Create & Manage Inspection Plans
- Defining and managing ranges by context
- Range versioning
- Mass updates from multi-level models
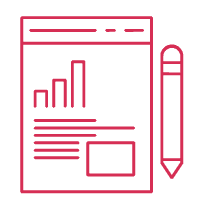
Production Checks and Inspection
- Automatic integration of production data
- Manual and automatic inspection data entry
- Operator-friendly interface
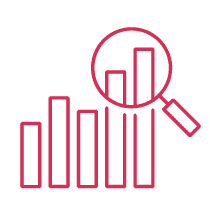
Total Traceability
- Registration of production batches and serial numbers
- Complete control and modification history
- Tracking users and actions taken
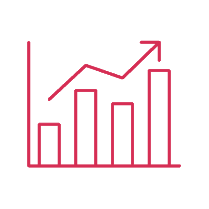
Real-Time SPC
- Real-time generation and updating of control cards (X-bar, R, P, NP...)
- Create and display histograms in real time
- Instant detection of drifts and anomalies
- Alerts and notifications in the event of non-compliance
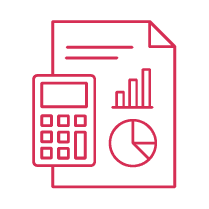
Calculation and Monitoring of Capability Indicators
- Calculation of Cp, Cpk, Pp, Ppk indices
- Capability index trend monitoring
- Analysis of process capability to meet specifications
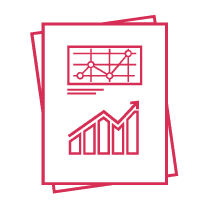
Customizable SPC Report
- Create control reports with customizable templates
- Export reports in various formats
- Integration of graphs and statistical data in reports
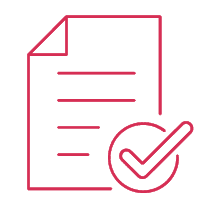
Compliance with Standards
- ISO 9001, ISO 9100, ISO 13485 compliant
- Compliance with FDA CFR 21 part 11 requirements
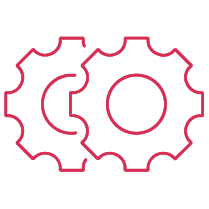
Integration with Existing Systems
- Accessible on Premise / Cloud, full web technology
- API for integration with MES, ERP and other production management systems
- Import and export data via CSV files, etc.
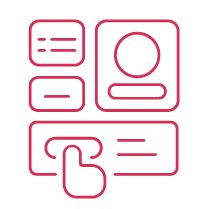
Intuitive User Interface
- Customizable dashboards
- Clear, intuitive view of control data
- Accessibility via various devices (PCs, tablets, smartphones)
Our SPC Methodology:
As-Needed Support!
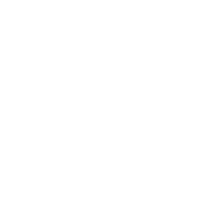
3 to 5 days of support
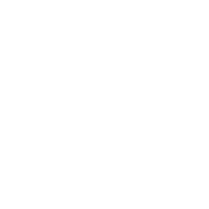
1 SPC license with measuring instrument connection
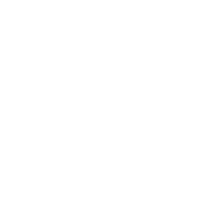
Weekly follow-ups by our project managers
Your Feedback
Read More

5 tips for successful control chart application
Many companies confuse Statistical Process Control with control charts... Control charts are just that: ...
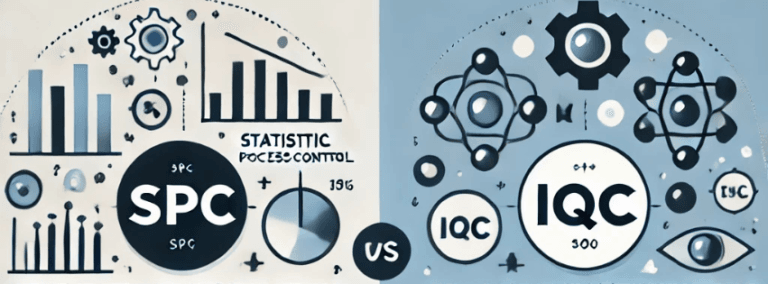
SPC or sampling control
When carrying out a production inspection, the question often arises as to the type of inspection. Which module should I ...
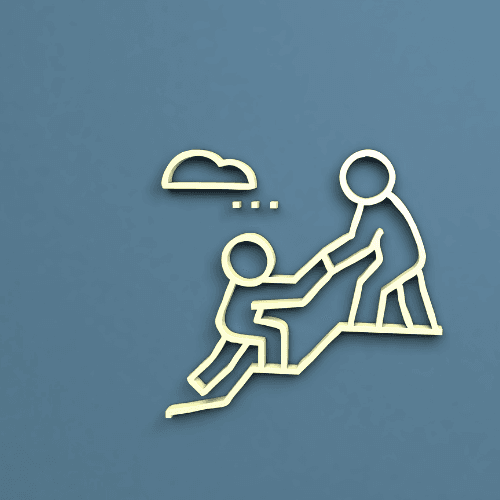
5 common SPC mistakes
Implementing SPC in production is anything but self-evident... If SPC is already well known ...
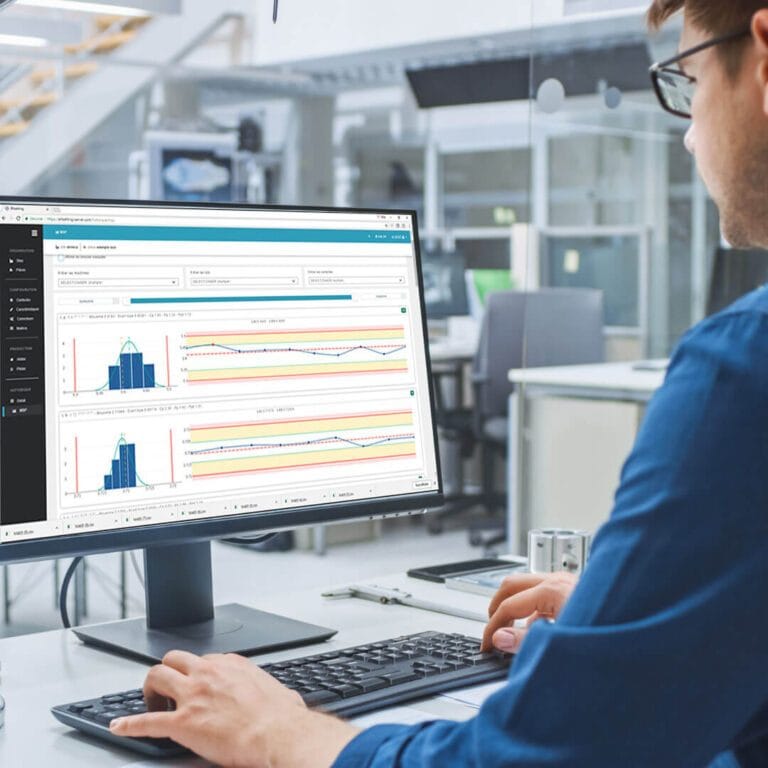
Does SPC still have a place in our workshops?
For over forty years, SPC has been an integral part of the production environment. It is ...
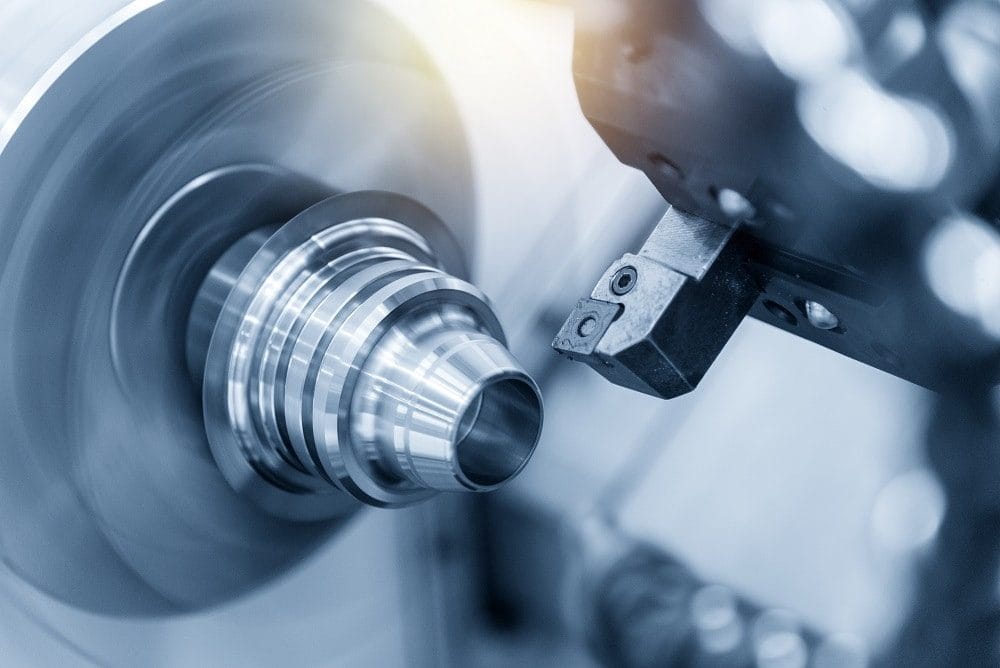