Desde hace más de cuarenta años, el SPC en los talleres de producción forma parte integrante del entorno. Es el método estadístico para supervisar los procesos de fabricación.
El principal objetivo de esta técnica es controlar el comportamiento de un proceso. El SPC se aplica en los talleres de producción mediante herramientas como los gráficos de control. De este modo, ayuda a reducir las tasas de rechazo al anticiparse a la no calidad.
El principio desarrollado por Shewart y tarjetas de control permite aplicar una acción al proceso sólo cuando está fuera de control. Mientras esté dentro de mis límites de control en verde, no corrijo mi proceso, y en cuanto salga de mi dispersión, lo corrijo.
El CPS es un método probado desde hace mucho tiempo, empezando por la industria del automóvil. Hoy en día, los fabricantes de diversos sectores siguen utilizando ampliamente el SPC. Sin embargo, los montajes son cada vez más complejos, con dimensiones interdependientes. Obviamente, esto hace que el trabajo del ajustador sea mucho más difícil que antes.
Estudio de caso : SPC en un taller de producción relojera
Tomemos como ejemplo un caso real de SPC de un taller de producción relojera.
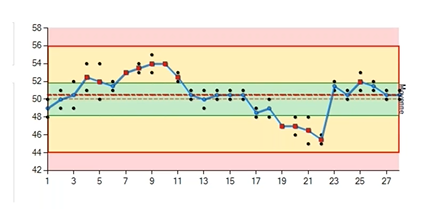
Si observamos este gráfico de control, podemos ver que no se ha seguido la regla sencilla y básica del SPC. Se ha permitido que el proceso se desvíe dentro de los límites de tolerancia. Es interesante entender por qué. Al profundizar en el tema y hablar con el ajustador de esta planta de producción, nos dimos cuenta de que esta dimensión repercutía en la siguiente. Si el colocador corregía esta cota, la siguiente sería mala. Así que, por decisión propia, el colocador se mantenía dentro de las tolerancias. Desgraciadamente, el resultado es una calidad que no siempre es óptima y, por tanto, no cumple los requisitos del cliente.
APC (Automated Process Control) como alternativa al SPC ante las dificultades de ajuste en los talleres de producción.
Ante estas dificultades, debemos encontrar una solución capaz de responder a los tres principales retos a los que se enfrentan los fabricantes hoy en día:
- Reto 1: dominar la capacidad a largo plazo
- Reto 2: ser capaz de gestionar piezas complejas en un entorno multidimensional
- Reto 3: integración en la cadena digital
Control automatizado de procesos (APC) es un concepto inventado bajo la dirección del Prof. Maurice Pillet por lal laboratorio SYMME de la Universidad Savoie Mont Blanc. Se trata de una evolución del SPC. El APC consiste en utilizar recursos informáticos para controlar un proceso de producción con el fin de obtener resultados de calidad mucho mejores que con el SPC tradicional. Mediante el ajuste simultáneo de decenas de correctores, el APC corrige las derivas utilizando una función de amortiguación derivada de un algoritmo de aprendizaje automático. De este modo, la corrección se desvía menos hacia los límites del tablero de control. Esto se debe a que la corrección se centra en la dimensión funcional objetivo. Como resultado, la calidad se controla a largo plazo.
Conclusión
Por supuesto, el SPC sigue teniendo su lugar en el taller. Pero ahora existen desarrollos que pueden ayudar al personal de puesta a punto a corregir procesos multidimensionales. Esta innovación se llama Control Automatizado de Procesos.