Depuis plus de quarante ans, le SPC dans les ateliers de production fait partie intégrante de l’environnement. Il s’agit de la méthode de suivi des procédés de fabrication par les statistiques.
L’objectif principal de cette technique est de surveiller le comportement d’un processus. Le SPC est appliqué dans les ateliers de production avec des outils tels que les cartes de contrôle. Il permet donc de réduire les taux de rebut par anticipation de la non-qualité.
En effet, le principe développé par Shewart et les cartes de contrôles permet d’appliquer une action sur le processus uniquement lorsque ce dernier est hors contrôle. Tant que je suis dans mes limites de contrôle en vert, je ne corrige pas mon process et dès que je sors de ma dispersion alors je corrige.
Le SPC est une méthode qui a fait ses preuves depuis longtemps à commencer par l’industrie automobile. Le SPC reste encore aujourd’hui largement utilisé par les industriels de différents secteurs. Cependant, les réglages sont de plus en plus complexes avec des cotes interdépendantes les unes des autres. Cela rend évidemment le travail des régleurs beaucoup plus difficile qu’auparavant.
Etude de cas : SPC dans un atelier de production en horlogerie
Prenons comme exemple un cas SPC réel issu d’un atelier de production en horlogerie.
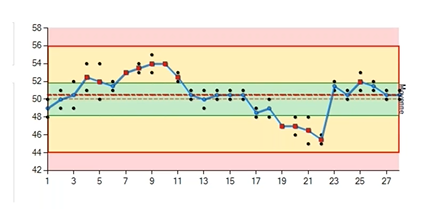
En observant cette carte de contrôle, on se rend compte que la règle simple et basique du SPC n’a pas été respectée. En effet, on a laissé dériver le process dans les limites de tolérances. Il est alors intéressant de comprendre pourquoi. En creusant et en discutant avec le régleur de cet atelier de production, nous nous sommes rendu compte que cette cote avait un impact sur la suivante. Si le régleur corrigeait cette cote, la suivante serait mauvaise. C’est donc par choix que le régleur est resté dans les tolérances. Malheureusement, ce fonctionnement abouti à une qualité qui n’est pas toujours optimale et qui ne répond donc pas aux exigences clients.
L’APC (Automated Process Control) comme solution de remplacement du SPC face aux difficultés de réglage dans les ateliers de production
Face à ces difficultés, il convient donc de trouver une solution capable de répondre aux trois enjeux principaux dont font face les industriels aujourd’hui :
- Enjeux 1 : être capable de maitriser la capabilité sur le long terme
- Enjeux 2 : être capable de gérer des pièces complexes dans un environnement multidimensionnel
- Enjeux 3 : s’intégrer dans la chaine numérique
L’Automated Process Control (APC) est un concept inventé sous la direction du Pr. Maurice Pillet par le laboratoire SYMME à l’Université Savoie Mont Blanc. Il s’agit d’une évolution du SPC. L’APC consiste à utiliser des moyens informatiques pour piloter un procédé de production afin d’obtenir de bien meilleurs résultats qualité qu’avec le SPC traditionnel. Assurant l’ajustage simultané de dizaines de correcteurs, l’APC corrige les dérives à l’aide d’une fonction d’amortissement issu d’un algorithme de machine learning. La correction dérive alors moins vers les limites de la carte de contrôle. Car la correction est centrée sur la cible de la cote fonctionnelle. Ainsi, la qualité est maîtrisée sur le long terme.
Conclusion
Le SPC à bien entendu toujours sa place au sein des ateliers. Mais il existe aujourd’hui des évolutions capables d’accompagner les régleurs dans les corrections des process multidimensionnels. Tout en s’intégrant à l’industrie 4.0 : cette innovation s’appelle l’Automated Process Control.